
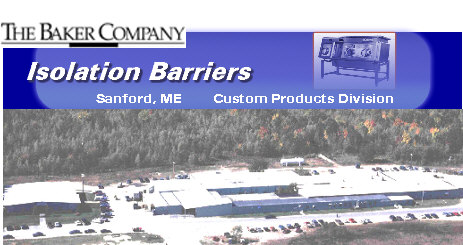
Known for building the first Biological
Safety Cabinet, Baker has an array
of aseptic and containment isolators to meet
your application.
The Baker Company has been a world leader in the field of Isolation and
Containment Technology for more than 50 years.
The reputation of the Baker design and construction is based on an
ISO9001
certified quality system and years of direct experience in
Pharmaceuticals and
Life Sciences applications. With Baker's renowned
expertise in Laminar Flow HEPA
filtration, containment technology,
unequaled microbiological test facilities
and stainless steel manufacturing,
you can be sure you are working with a
full-service company able to
support any isolation project you may have.
Testing
Rigorous
Testing to
Verify Performance
While many companies claim they can build a special
containment Isolator,
it is another thing to prove it works! Because of Baker's
total dedication and
commitment to your safety, The Baker Company has
established the Isolator
Industry's most extensive testing laboratories,
equipment, and expert
personnel to assure that every unit shipped from their
facility meets or
exceeds all performance criteria.
Baker may challenge a system with Bacillus subtilis
var.Niger spores in our
unique Microbiological Testing Laboratory to assure
sterility or simulate worst
case air flow conditions in our computerized Air
Flow Management Laboratory.
Due to Bakers' stringent testing process, you are
assured of a final product
you can trust. As part of your documentation package,
you are provided with
all protocols and testing results necessary to validate
the performance of your
new equipment. Detailed IQ, OQ and PQ services can be
provided by Baker
when required for FDA approval and validation.
Advanced In-house
Testing Capabilities
- NSF-49
- ASHRAE/ANSI 110
- Mass Spectrometer Helium Leak Checking
- HEPA Filter Leak Checking
- Microbiological Aerosol Challenges
- Sterility/Decontamination Effectiveness
- Particulate Counts/Federal Standard 209E
- Passivation Assurance
- PSL Challenges
- Sound, Illumination, Vibration
- Vapor Phase Hydrogen Peroxide Cycle Times
Validated Applications:
Aseptic Liquid and Powder Filling Lines
Sterility Testing
Potent Weigh & Dispense
QC Sampling
Radiolabel Formulation
Centrifuge Enclosures
HEPA Filtered Downflow Booths
Isolation integrated with:
Cappers
Filter Dryers
Fillers
Grinding Mills
Lyophilizers
Tank Charging
Vacuum Ovens
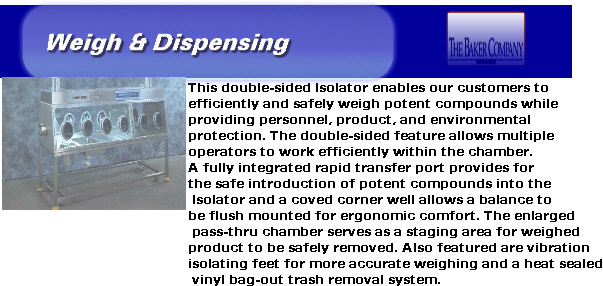
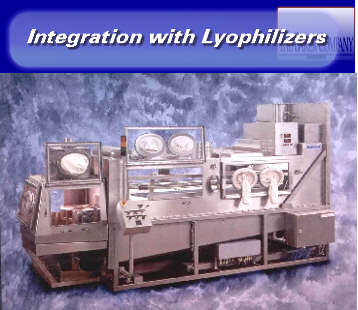
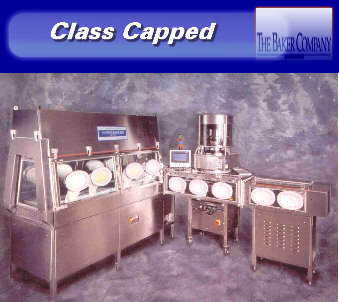
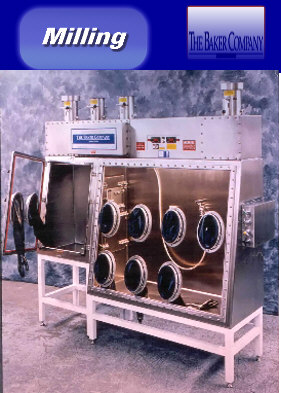

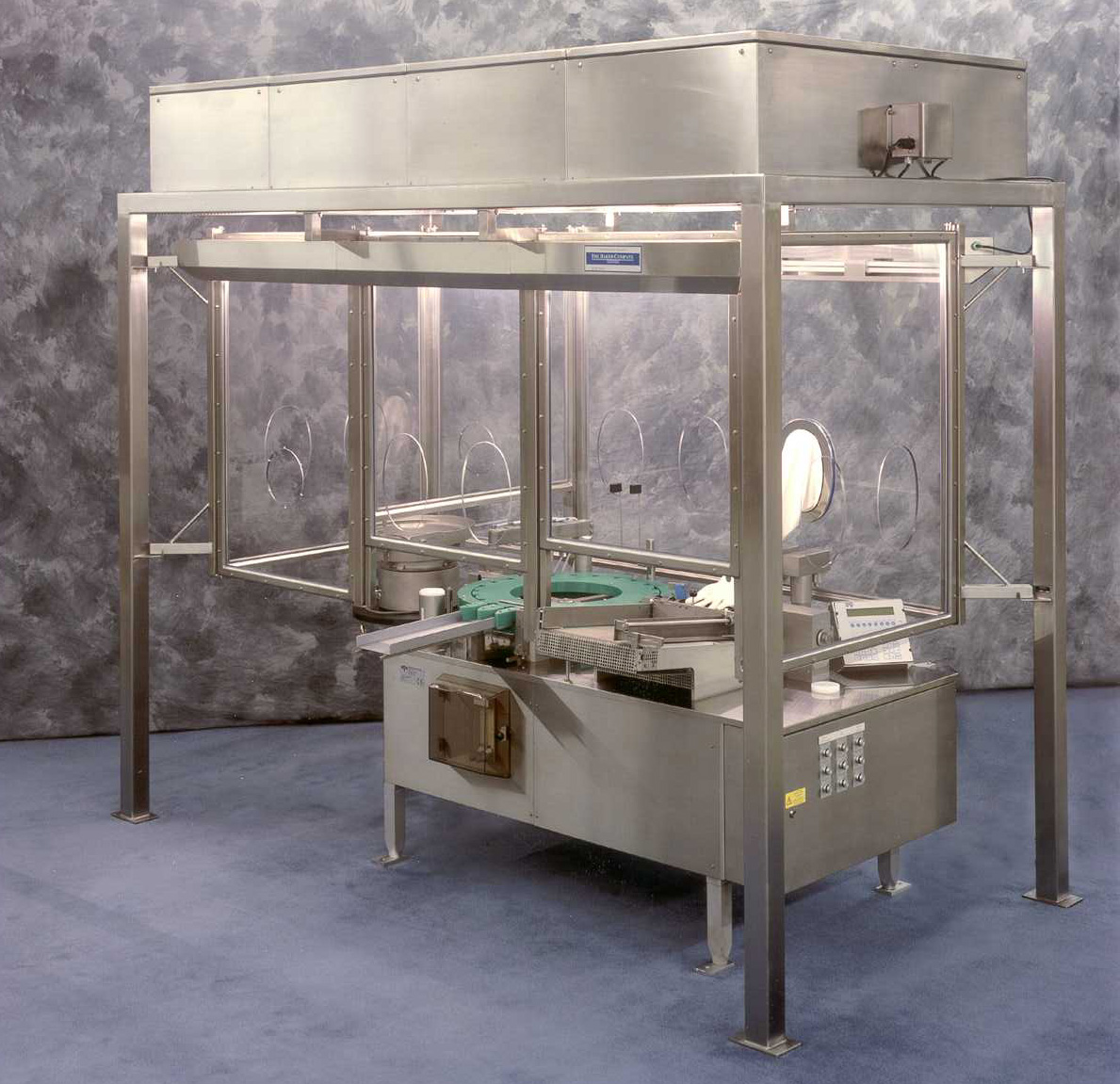
ParenteralGARD®
The benefits of the ParenteralGARD® include:
-
Allows the operator to
intervene in the aseptic process without
compromising asepsis.
-
Using glove ports, operations
personnel are able to keep all barrier
panels closed and in place.
-
Sanitization with
an aerosol spray sanitant, eliminating the need for
costly VHP generators, and
airtight enclosures.
-
Used within a conventional
cleanroom - no need to construct new
facilities.
-
Personnel use familiar
gowning techniques and the ParenteralGard®
provides a secondary barrier
between the operators and the aseptic
process.
This innovative concept provides many of the benefits of a
complete Barrier
Isolation System, but without the rigorous and risky validation
requirements,
at a very attractive price. Dramatic improvements in Sterility
Assurance Levels,
up to one hundred times cleaner when compared to a
conventional class 100
cleanroom with a gowned operator are readily achieved.
Component transfer
systems (including stoppers), use the novel, patented rapid
transfer port
"Biosafe" by IDC.
These low cost and light weight ports are practical and
properly engineered to
eliminate the "ring of concern" which is common to
rotary seal
ports.
This integrated system is designed to provide significant,
reliable reduction
in both total airborne particulates and viable counts in the
critical zones of
your aseptic process. A ParenteralGARD® can be delivered to
your site in
a fraction of the time, and at a much lower cost than sealed
isolators.
Find out how you can upgrade your aseptic process in real time, for
real money.
Questions & Answers
A. ParenteralGARD® is a novel approach to
reducing the microbiological
and total particulate levels and improving quality
assurance in ANY process
run under aseptic conditions. Working within a
conventional cleanroom, the
ParenteralGARD® could be the effective, and
practical answer to the ongoing
efforts many companies are struggling with
today: To buy an isolator,
or not to buy....
A. ParenteralGARD® takes advantage of a
simple fact that the "dirtiest"
element within any aseptic process is
the human operator. The same basic
technology has been used for over 25 years to
try and provide some sort of
boundary between the humans and the product being
processed. Unfortunately,
conventional curtains and panels must still be moved
out of the way to allow
the operations personnel access to the equipment when
adjustments are
required. The ParenteralGARD® solves that problem by allowing
the operators
to have access to the equipment WITHOUT opening the
ParenteralGARD®
panels. Therefore, the aseptic process is protected from
exposure to human
and equipment borne particulate load, whether viable or not.
A. While the concept of sealed isolators,
running in unclassified areas in a
pharmaceutical plant, has been actively
explored since 1992, the number of
successful installations of such technology
is still quite low. Someday, the cost
effectiveness and practicality of aseptic
processes running inside sealed isolators
in low cost plant space may be proven.
If you need to have a process running
NOW, and at a REASONABLE COST, take a
close look at the ParenteralGARD®.
A. The cost of investing in, or upgrading a
conventional Class 1000 (Grade B)
cleanroom and installation of a ParenteralGARD
A. An isolator is not a sterilizing device!
At best, it can only reduce the
likelihood of adventitious contaminants entering
into an aseptic process.
Isolator operation requires the same care and even more
operator training,
compared to conventional aseptic processes, to run
successfully. The elegant
simplicity of the ParenteralGARD® allows you to take
advantage of your current
infrastructure and experienced personnel to IMPROVE
the sterility assurance
level of your aseptic processes.
A. The development of the ParenteralGARD®
has been underway for many years.
The apparent simplicity is deceptive;
extensive engineering studies and testing
were required to create the versatile,
successful ParenteralGard® system.
There is far more to a ParenteralGARD® than
gloveports and plastic panels.
Let BAKER and VICTOR INTERNATIONAL show
you how the ParenteralGARD® can improve your process
at an affordable
price, in the same millennium
that you started the project!
|